The Challenges and Best Practices of Cold Weather Welding
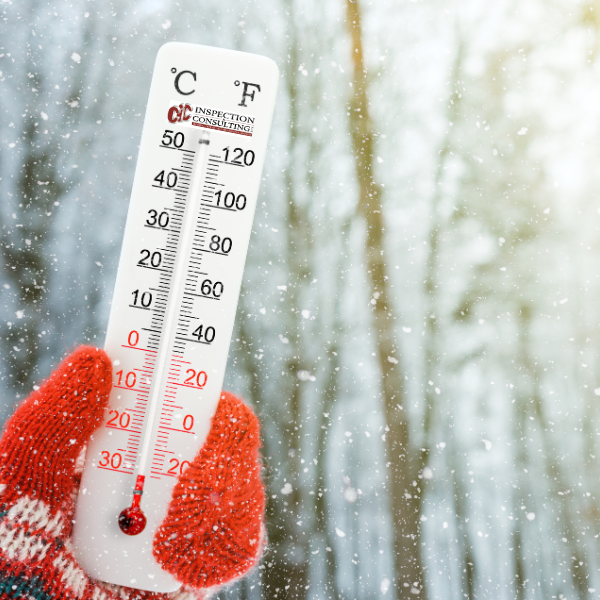
Welding is a precise and demanding task, requiring the right conditions, equipment, and techniques to ensure strong, reliable welds. When temperatures drop, however, welding becomes even more challenging. Cold weather can have significant impacts on the welding process, from altering the properties of the materials being welded to affecting the behavior of the welding equipment itself. Understanding these challenges and implementing best practices can make the difference between a successful weld and one that fails under stress.
The Impact of Cold Weather on Welding
Cold weather introduces several issues that can affect the quality and durability of a weld. Some of the primary challenges include:
1. Material Brittleness: Cold temperatures can make materials, especially metals, more brittle. This brittleness increases the risk of cracking during and after the welding process. Metals like carbon steel, which are commonly used in construction and manufacturing, are particularly susceptible to this issue.
2. Condensation and Moisture: Cold environments can cause condensation to form on metal surfaces. Moisture on the surface of the material can lead to hydrogen entrapment in the weld, which can result in hydrogen-induced cracking (HIC). Ensuring that materials are dry and free from condensation before welding is critical.
3. Increased Heat Loss: Cold temperatures cause the weld pool to cool rapidly, which can lead to insufficient fusion between the base materials and the weld metal. This rapid cooling can also increase the hardness of the weld area, making it more prone to cracking.
4. Equipment Performance: Welding equipment, such as power sources, wires, and torches, can be affected by cold weather. Cables can become stiff, and gas flow rates can be altered, leading to inconsistent welds.
Best Practices for Cold Weather Welding
To overcome these challenges, welders and companies can implement several best practices when working in cold weather:
1. Preheat the Material: Preheating the material before welding is one of the most effective ways to prevent cracking and ensure proper fusion. Preheating reduces the cooling rate, allowing the weld to cool more slowly and reducing the risk of brittleness.
2. Use Low-Hydrogen Electrodes: To minimize the risk of hydrogen-induced cracking, it's essential to use low-hydrogen electrodes or filler materials. These materials are designed to reduce the amount of hydrogen introduced into the weld, making them ideal for cold weather applications.
3. Maintain Dry Conditions: Before welding, ensure that all materials are dry and free from condensation. This may involve storing materials in a heated environment or using portable heaters on-site to eliminate moisture.
4. Protect the Weld Area: Use windbreaks or enclosures to protect the weld area from cold winds, which can exacerbate heat loss. In some cases, insulating blankets or heated tents may be necessary to maintain an optimal welding environment.
5. Regularly Inspect Equipment: Cold weather can affect the performance of welding equipment, so it's important to inspect cables, torches, and power sources regularly. Ensure that gas flow rates are consistent and that all components are functioning correctly.
The Importance of Cold Weather Welding Procedures
Given the challenges posed by cold weather, it is crucial for welding contractors to have specific cold weather welding procedures in place. These procedures serve as a guideline for welders to follow, ensuring that every weld meets the necessary quality and safety standards, even in adverse conditions. Contractors who have established procedures can better manage the risks associated with cold weather welding, from preventing material cracking to ensuring that all equipment operates correctly.
Moreover, having cold weather welding procedures in place demonstrates a contractor's commitment to quality and safety. It assures clients that the contractor is prepared to handle the complexities of cold weather welding, reducing the likelihood of weld failures and costly repairs. These procedures also help in training and equipping welders to adapt to different environmental conditions, leading to more consistent and reliable outcomes.
Cold weather welding presents unique challenges, but with the right approach and techniques, these challenges can be effectively managed. By preheating materials, using appropriate electrodes, maintaining dry conditions, and protecting the weld from the elements, welders can produce strong, reliable welds even in the most demanding environments. For welding contractors, having cold weather welding procedures in place is not just a best practice; it is essential for ensuring high-quality results and maintaining client trust.
For companies like CIC Inspection & Consulting, which have decades of experience in materials testing and welding inspection, understanding and mitigating the risks associated with cold weather welding is crucial. Our expertise ensures that our clients receive the highest quality welding services, regardless of the environmental conditions. Whether you're working in frigid temperatures or under ideal conditions, our team is here to support your welding and inspection needs with precision and reliability.
For more information, assistance on your project, or an inspection quote, please contact us at 780-468-4593 or by email at reception@cicinsection.com. We're here to ensure your projects meet the highest standards, no matter the weather.