How many Welding Inspection Techniques are there?
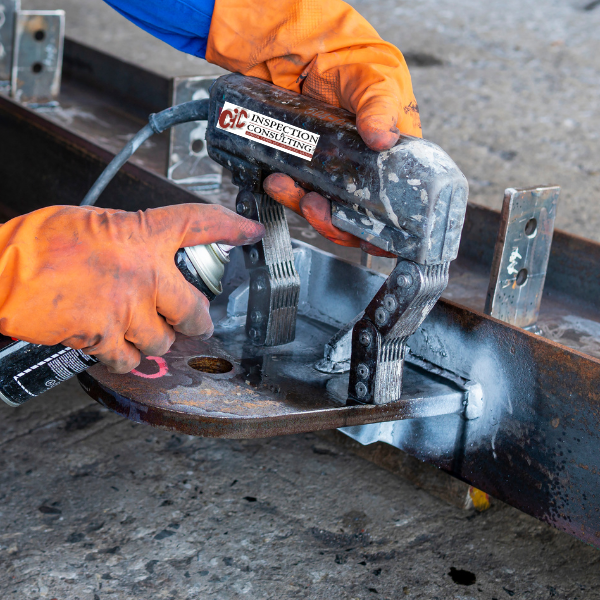
Here are 7 Essential Nondestructinve Testing Techniques You Need to Know.
Welding plays a crucial role in the Infrastructure and Oil & Gas industries. From construction of steel structures to manufacturing, where the quality and integrity of welds are of utmost importance. Ensuring weld quality on your project often requires a range of welding inspection techniques, each offering distinct advantages and applications.
This article provides you with a look at the various welding inspection techniques, helping you understand their importance and how they are utilized in practice.
Visual Inspection (VT)
Visual Inspection is the simplest and most commonly used method of weld inspection. It involves examining the weld with the naked eye or using optical aids such as magnifying glasses.
This inspection technique is primarily used for the initial assessment of welds to detect visible defects like cracks, porosity, and incorrect weld size.
Advantages of Visual Inspection (VT): It is straightforward, quick, and cost-effective.
Limitations of Visual Inspection (VT): It cannot identify internal flaws
Radiographic Testing (RT)
Radiographic Testing employs X-rays or gamma rays to penetrate the weld metal in order to produce an image on a radiographic film.
This inspection method is ideal for identifying internal defects such as porosity, slag inclusions, cracks and lack of fusion to name a few.
Advantages of Radiographic Testing (RT): It provides a permanent record of the weld and detailed imaging of internal flaws.
Limitations of Radiographic Testing (RT): Radiographic testing is expensive, requires specialized equipment and safety precautions, and interpreting the results can be complex.
Ultrasonic Testing (UT)
Ultrasonic Testing uses high-frequency sound waves to detect flaws within the weld. Sound waves are transmitted into the material, and reflections from flaws hidden inside the weld metal or base metal are detected and analyzed against an acceptance criterion.
Ultrasonic Testing It is used for detecting internal weld defects and is also used for measuring material thickness.
Advantages of Ultrasonic Testing (UT): This technique is highly sensitive, capable of detecting very small defects, and provides immediate results.
Limitations of Ultrasonic Testing (UT): It requires skilled operators and precise calibration, and it may struggle with complex geometries.
Magnetic Particle Testing (MT)
Magnetic Particle Testing involves magnetizing the weld area and applying ferromagnetic particles. Defects create magnetic leakage fields, attracting the particles and making the flaws visible.
This method is used for detecting surface and near-surface flaws in ferromagnetic materials.
Advantages of Magnetic Particle Testing (MT): It is simple, relatively inexpensive and can detect both surface and shallow subsurface defects.
Limitations of Magnetic Particle Testing (MT): It is limited to ferromagnetic materials and may require surface preparation.
Dye Penetrant Testing (PT) (Also known as Liquid Penetrant (LPI))
Dye Penetrant Testing involves applying a liquid dye to the weld surface, allowing it to penetrate defects. A developer is then used to draw out the dye, highlighting any flaws.
This technique is effective for identifying surface-breaking defects in non-porous materials.
Advantages of Dye Penetrant Testing (PT): It is simple, cost-effective, and suitable for a wide range of materials.
Limitations of Dye Penetrant Testing (PT): It only detects surface defects and requires thorough cleaning before and after testing.
Eddy Current Testing (ET)
Eddy Current Testing utilizes electromagnetic induction to detect flaws in conductive materials. Changes in the eddy current flow indicate the presence of defects.
This method is used for surface and near-surface defect detection in conductive materials.
Advantages of Eddy Current Testing (ET): It is a non-contact method, highly sensitive, and can be automated for continuous monitoring.
Limitations of Eddy Current Testing (ET): It is limited to conductive materials and may struggle with complex geometries and deep flaws.
Acoustic Emission Testing (AE)
Acoustic Emission Testing monitors sound waves emitted by a material under stress. The sudden release of energy from a defect under stress creates an acoustic emission event that can be detected.
This technique is used for real-time monitoring of structures under load to detect crack growth and other defects.
Advantages of Acoustic Emission Testing (AE): It can detect active defects, provides real-time monitoring, and covers large areas.
Limitations of Acoustic Emission Testing (AE): It requires a quiet environment, and interpreting the results can be complex.
A thorough understanding of various welding inspection techniques is essential for ensuring the integrity and safety of welded structures. Each technique has its unique advantages and limitations, making it crucial to select the appropriate method based on the project's specific requirements. By combining these techniques, inspectors can achieve a comprehensive assessment of weld quality, ensuring reliability and longevity in their applications.
In the ever-evolving field of welding inspection, staying informed about the latest advancements is key to maintaining high standards of quality and safety. Embracing the right techniques and technologies ensures that welded structures remain robust and dependable, reflecting excellence in welding practices.